PROCOMP Project LH2 tank
Thermoplastic composite upper stage LH2 tank
The demo tank of the PROCOMP project utilizes ultrasonic welding technology for field integration and assembly during the automated fiber placement (AFP) process using carbon fiber/LMPAEK tape
The number of launches is expected to exceed 1,000 by 2040, and one of the main drivers of this growth is SpaceX's technological innovation.
The company used the Falcon 9 Heavy to spend an average of $2,500 per kilogram on launch costs, which were $18,500 per kilogram between 1970 and 2000,
Furthermore, we were able to drastically reduce it to 1,500 dollars per kilogram.
-
PROCOMP demonstrator tank
Automated layup and in-situ consolidation
Production of the PROCOMP demonstrator tank (above) was carried out using the robot winding system and aluminum tools as a starting point for AFP in situ dom #1 (below).
-
100% inline inspection
PROCOMP Laser Line Inspection
During PROCOMP laser line inspection, AFP PROCOMP developed an in-line inspection system using laser lines and special cameras to detect gaps and redundancies during AFP in-situ consolation.
-
Future development, LH2 aircraft
Successful Demo Product
The manufacturing process from load calculation to tank design, AFP programming, welding of both parts, and integration of the propellant management system in the tank is highly reliable.
Future development, TEAM PROCOMP
Work on topics that are still unresolved
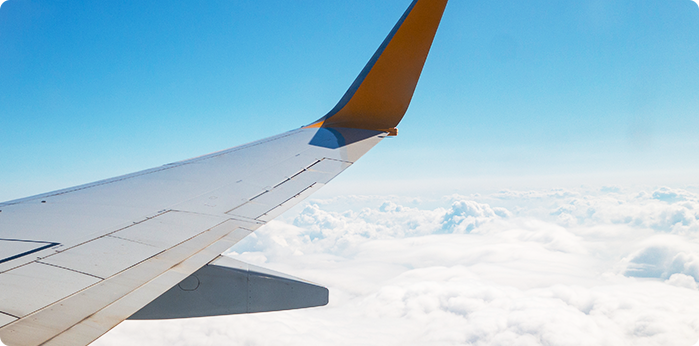
The manufacturing process from load calculation to tank design, AFP programming, welding of both parts, and integration of the propellant management system in the tank is highly reliable
We've achieved a lot, but we're already working on other projects on topics that we haven't solved within PROCOMP, and we're moving in a forward-looking direction.
In addition, large-scale German funding for H2 storage in aircraft has recently been launched. It is targeting flight testing in the near future and thermoplastic composites will play an important role in the long run.