Motorcycle brake disc cover
Motorcycle brake disc cover showing the possibility of KTM Technology's Conexus bonding technology and flax fiber composite material
Using Conexus bonding technology developed by KTM Technologies and flax fiber composite materials
Motorcycle brake disc covers are a combination of innovative technology and materials that have proven their excellence by winning several awards.
Conexus technology focuses on bonding composite materials more robustly and efficiently through special bonding methods.
In addition, flax fiber is in the spotlight as an eco-friendly material while providing lightweight and excellent strength.
-
Conexus
Adhesive-free multi-material bonding solution
In motorsports and various markets, thermosetting composite material parts are often combined with parts made from other materials such as unenhanced plastic or metal.
For multi-material bonding of thermosetting composite materials, mechanical fastening materials or adhesives are generally used.
-
Brake Cover
Carbon fiber first step
KTM started coupon level testing for various fiber and plastic parts combinations before applying Conexus technology to brake disc covers.
The brake disc cover project was launched to demonstrate the Conexus technology and is currently in series production at KTM in carbon fiber/epoxy versions.
-
Carbon fiber brake disc cover
First iteration
Early carbon fiber/epoxy brake disc covers have successfully demonstrated technology for end-use parts.
KTM Technologies has since returned to the design stage to use more sustainable materials.
Additional simulations were performed to ensure good filling and temperature distribution and avoid deformation during the injection molding process of the coupling layer.
More sustainable flax fiber version
How to reduce the overall carbon footprint of the component and create a more sustainable version
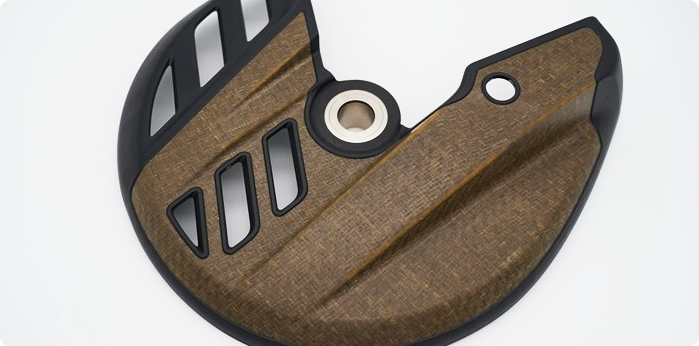
By switching from carbon fiber to flax fiber, the CO2 footprint of the material can be reduced by up to 60%.
Conexus technology enables you to produce aesthetic, high-performance parts on the one hand, and sustainability goals on the other
We can easily apply other fibers or thermoplastic materials using already established manufacturing methods.
It also has innovative bonding technology ready to go to market, making it easy to adapt to the needs of all customers without additional machine investment.
Sealing system
Magnum Venus Products (MVP) Develops Innovative Reusable Sealing System
The 'Secure Vacuum Bag Seal' (SVB Seal) is a reusable double sealing system.
This system replaces single-use sealing tape, which is used in vacuum injection closed mold processes.
SVB Seal has the advantage of reducing consumable costs and waste, reducing time and labor demands, and improving the quality and consistency of parts.
Advantages of SVB Seal
How to reduce the overall carbon footprint of the component and create a more sustainable version
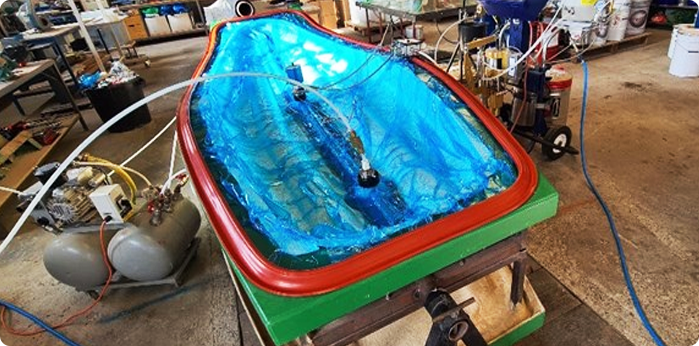
In traditional vacuum injection processes (VIPs), a sealing tape known as tape is used to hold the plastic bag around the mold.
These sealing tapes are disposable and require a lot of labor to apply due to folding and air leakage due to wrinkles in the bag, but SVB Seal removes wrinkles and produces air leakage-free sealing each time.
In addition to reducing consumable waste, hundreds of parts can be manufactured with a single SVB seal, resulting in significant cost savings for manufacturers
SVB Seal is designed to fit into a groove created around the mold, and the setup is the same as that of a typical vacuum bag process.
Instead of applying sealing tape to seal the bag around the mold, the bag is secured under the first half of the SVB seal in a groove in the mold flange.
Once the first half is sealed, the second half is added, vacuum is applied to the mold, air leak-free sealing and consistent injection.